The Coil Conundrum
Why Clean Coils Are Critical
If you manage HVAC systems across multiple commercial locations, understanding the importance of coil cleanings is crucial to maintaining efficient and reliable equipment. Whether you oversee retail stores, restaurants, banks, or healthcare facilities, proper coil maintenance can significantly impact system performance, energy costs, and overall comfort. Here's what you need to know.
What Are HVAC Coils and Why Do They Need Cleaning?
HVAC systems contain two primary types of coils: evaporator coils and condenser coils. These coils are responsible for heat transfer in your system, helping to cool indoor spaces and release heat outdoors. Over time, these coils accumulate dirt, dust, grease, and debris, which restrict airflow and diminish heat transfer efficiency.
Routine coil cleaning is essential to prevent buildup that can reduce system performance, increase energy consumption, and lead to costly repairs or premature equipment failure.
What Problems Do Coil Cleanings Prevent?
Failing to clean your coils can lead to several issues, including:
- Reduced Cooling Efficiency: Dirty coils struggle to transfer heat effectively, forcing your system to work harder and consume more energy.
- Increased Energy Costs: A system with clogged coils must run longer cycles to maintain desired temperatures, driving up your energy bills.
- Frozen Evaporator Coils: Dirt buildup restricts airflow, which can cause evaporator coils to freeze, resulting in system shutdown and costly repairs.
- Compressor Failure: Restricted heat transfer can cause the compressor to overheat and fail, one of the most expensive HVAC components to replace.
- Poor Indoor Air Quality: Dust and contaminants on coils can circulate through your system, compromising indoor air quality.
How Often Should Coils Be Cleaned?
Determining the ideal cleaning frequency depends on several factors:
- 1. Location:
- Urban Environments: Units in city areas may accumulate more dirt and debris due to pollution, requiring more frequent cleaning.
- Coastal Locations: Systems near the ocean may experience salt buildup, which corrodes coils and necessitates frequent cleanings to prevent damage.
- Dusty or Industrial Areas: Locations near construction zones, factories, or warehouses are prone to faster coil contamination.
- 2. Type of Business:
- Restaurants: Due to grease, oils, and airborne particles from cooking, HVAC systems in restaurants require frequent coil cleanings—often 2-4 times per year.
- Retail Stores and Offices: Unless located in high-traffic or pollution-heavy areas, these locations can typically perform coil cleanings on an as-needed basis rather than on a fixed schedule.
- Healthcare Facilities: Clean air is critical in medical environments, so coil cleanings may need to happen more frequently to maintain air quality standards.
- 3. Equipment Use and System Load:
- Units that run year-round or are heavily relied upon for temperature control may require more frequent cleanings to sustain optimal performance.
Signs Your Coils Need Cleaning
Even if you follow a routine maintenance schedule, there are signs that indicate your coils need attention:
- Unexplained increases in energy bills
- Reduced cooling or heating performance
- Longer system run times
- Visible dirt, dust, or debris on the coils
- Unusual odors or reduced indoor air quality
What Happens if You Skip Coil Cleanings?
Neglecting coil cleanings can have costly consequences:
- Energy consumption can increase by up to 30% due to reduced efficiency.
- Your system's lifespan may be reduced, leading to costly equipment replacements.
- Frequent breakdowns and expensive repairs are more likely.
- Occupants may experience discomfort due to inconsistent temperatures or poor air quality.
Protect Your Investment with Proactive Maintenance
Regular coil cleanings are a small investment that pays off in improved efficiency, lower energy bills, and longer equipment life. By tailoring your coil cleaning schedule to your location, business type, and equipment use, you can ensure your HVAC systems stay reliable and effective year-round.
If you're unsure how often your HVAC coils should be cleaned, partnering with a trusted HVAC provider can help you develop a maintenance plan that meets your site's unique needs. Proactive care today can save you from costly repairs and downtime tomorrow.
For even more information on the essential procedures for cleaning condenser coils at: https://www.achrnews.com/articles/154681-basic-steps-for-hvac-coil-cleaning
Have thoughts or experiences with coil cleanings at your facilities? Drop a comment below and let us know how you handle HVAC maintenance at your locations. We’d love to hear from you!
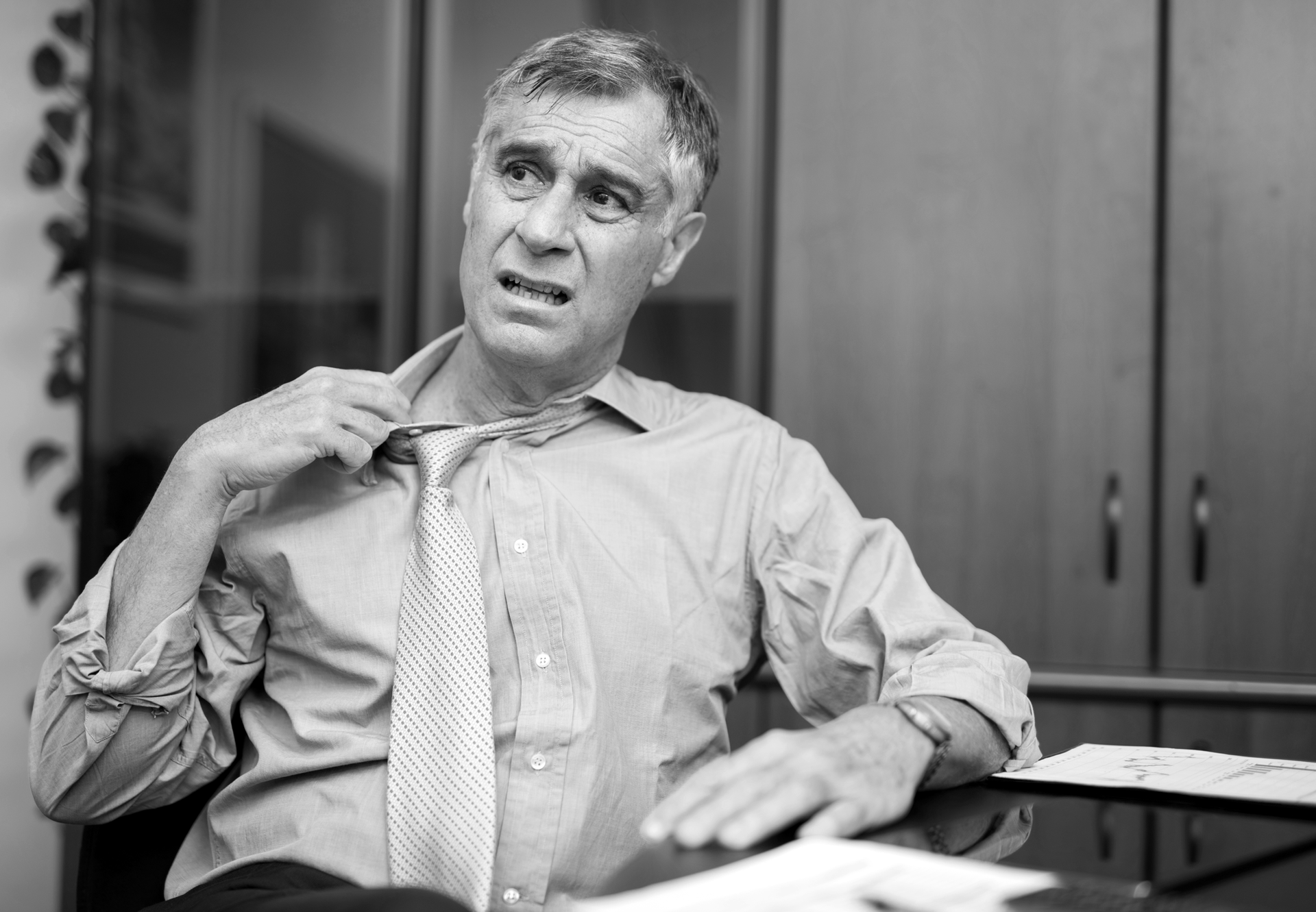
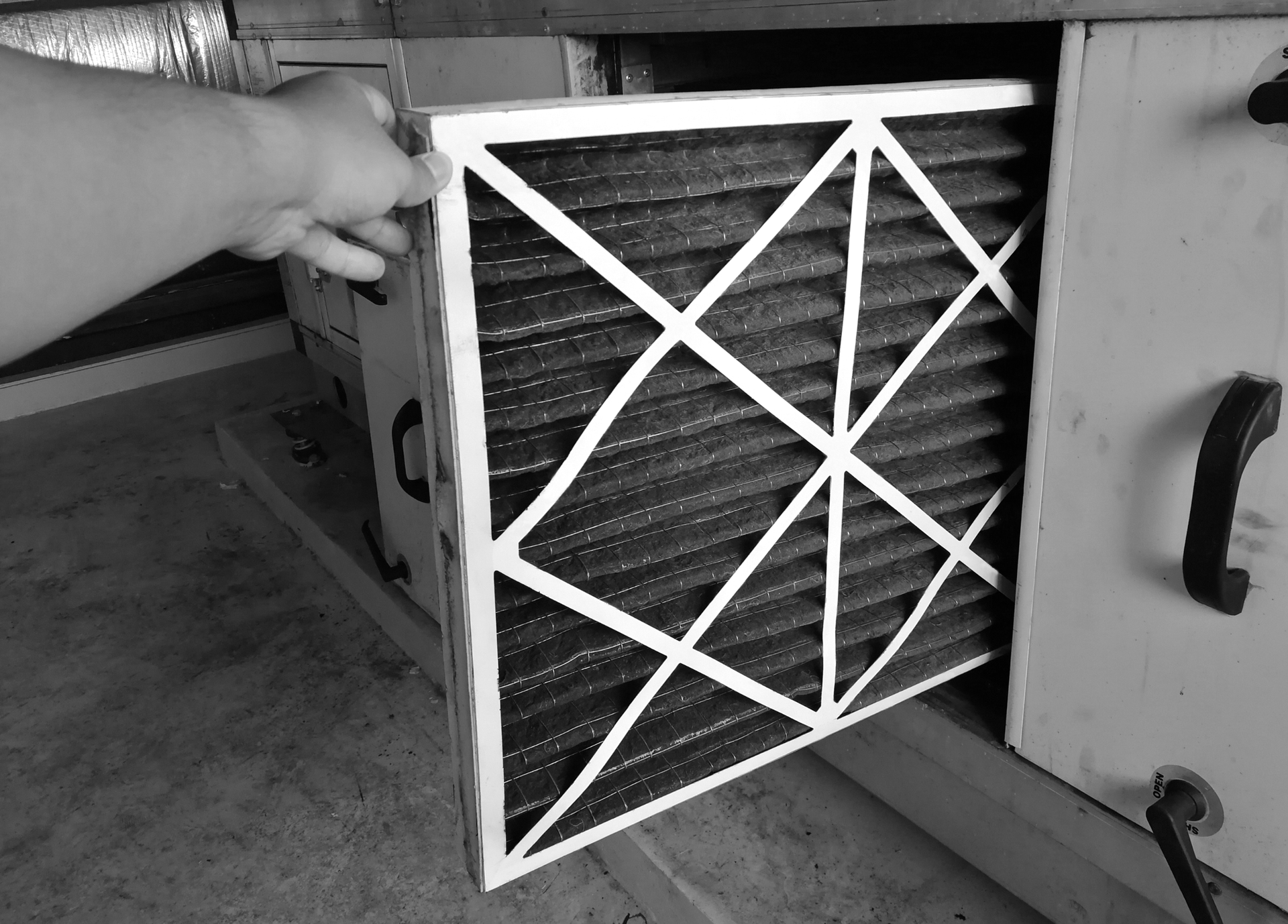
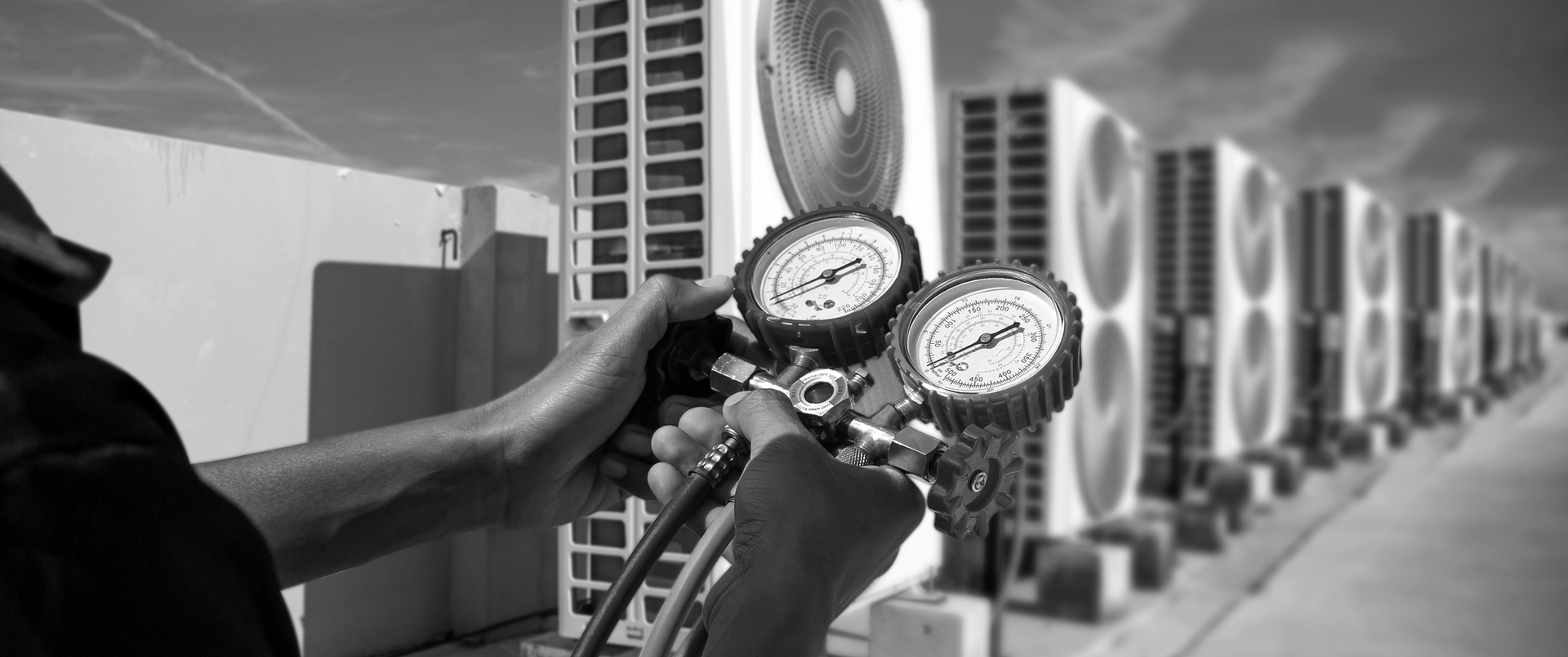